Procurement in construction is a cornerstone of any successful project, but some people are unsure as to what it entails. While the term “procurement” is all about acquiring the necessary resources to get a job done, the truth is that construction procurement is a significantly more involved endeavor. It involves sourcing materials, adhering to budgets and schedules, and using the most suitable parties for the work. Construction procurement also requires an understanding of how acquiring these resources will affect your bottom line.
What is Procurement in Construction?
Procurement in construction can be thought of as the assembly stage, or the “getting ready” step prior to construction commencing. For example, if you wanted to paint a painting, you’d have to get all your supplies and materials together ahead of time. You would need an easel, a palette, paint brushes, the paint itself, a canvas, and the object you wanted to paint. You’d also need a space suitable for painting, have carved out the time necessary to complete the painting, and would have to ensure that the conditions in which you would be painting were suitable for actual work. What’s more, you would need to make sure that you, the painter, was up for the job and was capable of completing it.
In a sense, procurement in construction is like assembling everything you would need for that painting. It involves obtaining all the necessary supplies, tools, resources, personnel, and information needed to complete a construction project according to a client’s specifications. Quantity, quality, and methodology all matter.
What is the Process of Construction Procurement?
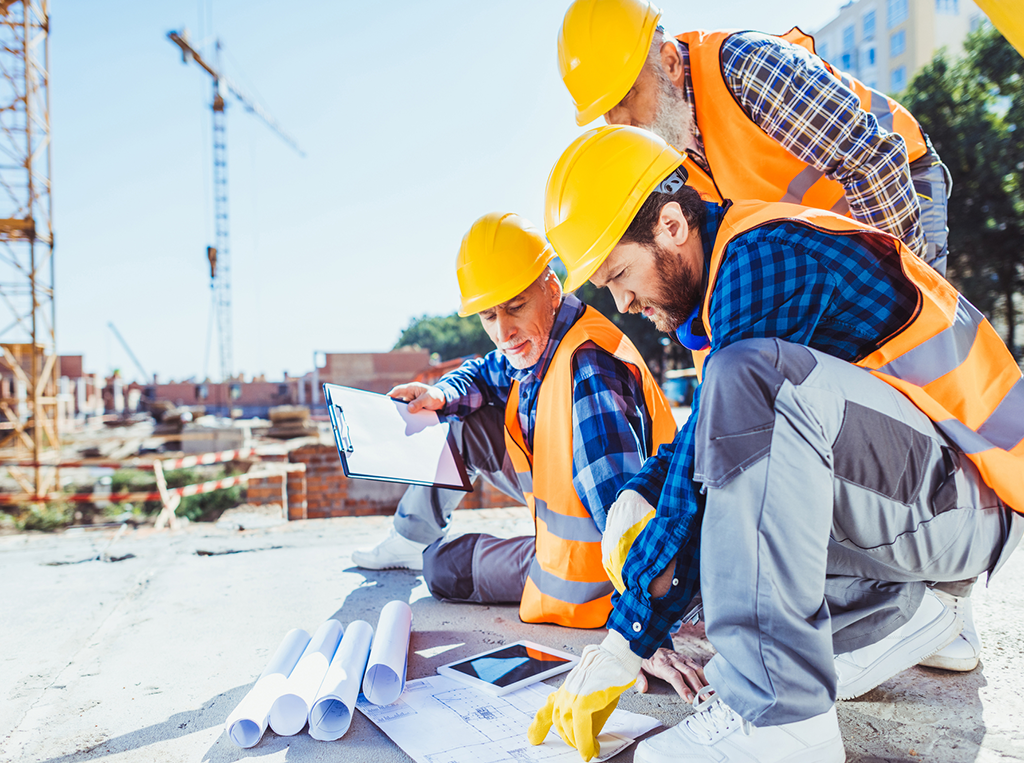
To understand the process of construction procurement, it’s important to know that there are various methods, each of which will affect how the process unfolds. With that said, while there are several construction procurement methods from which clients can choose, the initial process of getting started generally remains the same.
- First, the client must identify the overall objective(s) of the project. This will include developing a scope and specifying their requirements.
- Once the scope has been identified, the next step is to work with the general contractor and/or engineering team to determine what materials, equipment, and services will be needed.
- Following this, a Request for Proposal (RFP) will be made available to potential suppliers so they can submit proposals.
- The general contractor will then choose the suppliers they want to work with and specify the materials they need, as well as quality, quantity, delivery dates, and other pertinent information.
- The procurement process will wrap up with the suppliers delivering the materials. At this point, the general contractor will inspect the resources to confirm that they meet the expectations.
If these five steps seem simplistic, that is because this is the construction procurement process if everything goes exactly according to plan. In reality, that is seldom the case. Regardless of the method, procurement in construction is rarely quite so straightforward. Instead, it is an iterative process that requires constant tracking, project monitoring, and adjustments. It is therefore imperative that clients partner with a trusted general contractor to lead the way.
Who Leads Procurement in Construction?
Several parties are involved in procurement in construction, the most prominent being the general contractor. The project manager from the general contractor is the one who oversees the bulk of procurement in construction. This person works to identify project requirements, choose vendors, negotiate contracts for subcontractors, manage budgets, and ensure that all materials, resources, and services are delivered according to the plan.
Best Practices for Procurement in Construction
When it comes to procurement for your construction project, it’s important to work with a general contractor that adheres to best practices. This means staying updated on industry trends and paying attention to the market. It also involves using relevant technology such as tracking software to keep all parties accountable and on task. At Gidel & Kocal, we embrace technology as a part of our innovative approach to delivering the most time and cost effective solutions.
Best practices for procurement in construction also means being smart about suppliers contractors use. Gidel & Kocal chooses suppliers based on track record, reputation, financial stability, and their ability to deliver on time and according to quality standards.
The right general contractor will have a clear understanding of the project’s scope, including quality expectations, specs, overall project objectives, the budget, and the timeline. They will prioritize transparency and promote a collaborative, communicative environment. General contractors with experience in procurement will have conflict resolution systems in place, will implement quality control checks and audits, and will always adhere to safety and regulatory compliance codes. Top of the line GCs will also factor in sustainability and environmental considerations, especially for projects like life science conversions.
Procurement in construction is not a one-size-fits-all solution. Instead, it’s client-specific, and should always be tailored to the client’s needs. Every project has a unique set of requirements. Gidel & Kocal’s expertise in procurement makes us the perfect partner for your commercial construction project in northern California.
Find out more about procurement in construction and how we approach it by reaching out to our team. Contact us at Gidel & Kocal today!