As a full-service construction firm in the Bay Area, we have seen all sorts of construction projects and approach methods. Regardless of the size, scope, and specifics of the project, our role as a general contractor is to find the most efficient and cost effective way to complete your project while upholding all quality and safety standards. How this pans out looks different for every project, which is where value management, value analysis, and value engineering come into play.
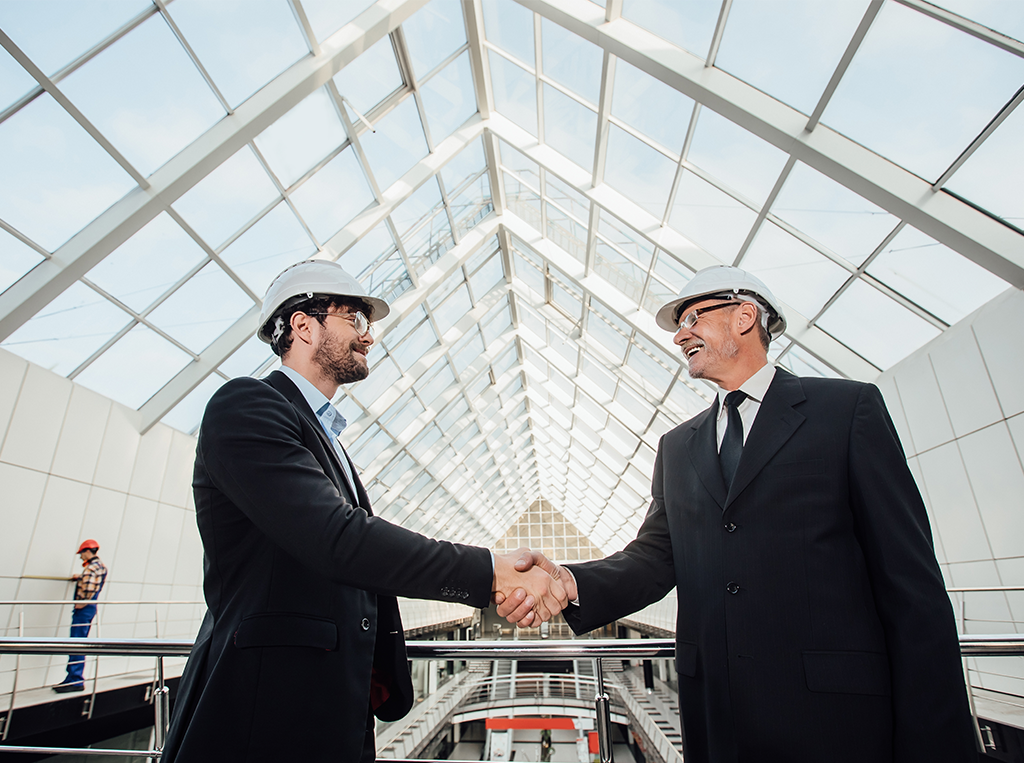
Value management is the umbrella term that encompasses both value analysis and value engineering, two integral components to the successful completion of a new build or renovation. Both are essential for the successful execution of a construction project, especially commercial construction. Understanding the purposes of value analysis and value engineering will help you continue along the right path as your construction project gets underway.
What is Value Analysis (VA) in Construction?
SAVE International® defines value analysis as “an assessment of a product that attempts to minimize its cost in relation to its functions.” While the definition mentions a product, value analysis can also be used as a mechanism for process optimization, such as with commercial construction.
Primarily concerned with the existing function of a service, value analysis aims to determine if something can be done at a lower cost without compromising quality or performance. It utilizes value engineering methodology to determine just how much the quality of a product or process can be improved. The essence of value analysis lies in evaluating how a service has been engineered and further optimizing it for function and ultimately cost reduction.
The six steps involved in value analysis include information gathering, function analysis, creative/brainstorming, evaluation, development, and the final presentation to stakeholders.
This leads to the next question: what is value engineering?
What is Value Engineering (VE) in Construction?
The goal behind value engineering is to improve a project’s value while reducing costs. This could result in redesigning and redeveloping entire systems, which could significantly impact both the current project as well as those in the future.
Value engineering calls on engineers, project managers, designers, and all those involved in a construction project to find alternative supplies that may lower the cost of production without compromising its quality. VE requires ongoing critical analysis throughout the lifecycle of a construction project, but is especially important during the pre-construction stages.
Key Differences Between Value Analysis and Value Engineering
It’s easy to see how value analysis (VA) and value engineering (VE) could be mistaken for one another, but their core tenets are what separate one from the other. Understanding their distinguishing features will help make you a more informed consumer, whether you’re an owner, a project manager, or any other involved party.
Features of Value Analysis
● Involves a 6-step process of information gathering, function analysis, creative exploration, evaluation, development, and presentation to stakeholders.
● Typically incorporated during the design and development stages of a construction project.
● Overall objective is to reduce costs while improving value and functionality.
● Analyzes the purpose of the project and what is needed to execute it.
Features of Value Engineering
● A 3-step process of planning, design, and methodology/approach.
● Cuts costs without compromising quality
● May involve redesigning and redeveloping systems.
● Strong focus on innovation.
The Steps of Value Analysis vs. Value Engineering
The information below can act as a cheat sheet or checklist for distinguishing value analysis from value engineering. The goal is to help you gain a better grasp on how to utilize these services in your next commercial construction project.
The Stages of Value Analysis
- Information gathering. The entire team meets to determine the overarching goal of the project and establish the project scope. During the informational stage, schedules, costs, budgets, risks, and additional administrative elements are ironed out for smooth execution.
- Function analysis. The team identifies the primary functions and secondary functions of a project. Primary functions express the overall purpose for why the project is being undertaken. Secondary functions may be considered additional benefits or byproducts.
- Creative. This is where new ideas get generated. Designers, engineers, and other involved parties may look at alternative methods for production or consider different supplies that can be used without sacrificing quality or value.
- Evaluation. It is during this stage that the risk vs. reward profiles of the creative ideas are analyzed for their potential to be put into action.
- Development. A clear plan of action outlines how the creative ideas will be put implemented
- Presentation. Stakeholders are presented with the findings, which may include brief documents, a risk analysis, a current worth analysis, advantages vs. disadvantages of using certain supplies vs. others, and more.
The Stages of Value Engineering
- Planning. During this initial stage, engineers and project managers define the key goals of the project as well as what will be needed to accomplish it. They will perform a functional analysis of the facility, review all supply and material options (as outlined in the value analysis component), and settle on a projected budget.
- Design. By reviewing the projected design plan, the value engineering team can iron out any last details related to structural designs, estimated costs, projected timelines for the project, and the suggested path for moving forward.
- Methodology. The methodology component encompasses all six stages of value analysis: information, function analysis, creative/brainstorming, evaluation, development, and presentation.
Construction can only begin once the presentation to the stakeholders has yielded a successful outcome. These strategies have proven that process orientation and optimization are the keys to cutting costs while upholding quality.
Experienced construction firms like Gidel & Kocal understand how to implement value analysis and value engineering. Our expertise in these areas will lend itself to the overall success of your commercial construction project and deliver an outcome you will be more than satisfied with. For additional information or to discuss working with us, please contact us today.